Automate vertical inspections with drones
With the rapid growth of drone industry, the interest from construction, engineering, real estate, and insurance communities in using UAS for building, roof, and infrastructure inspections has increased significantly. This can range from inspecting buildings, bridges, chimneys, open pit walls, dams as well as communications and electrical infrastructure like cell towers or wind turbines.
The result of these UAV surveys is a set of images captured with a specific forward and side overlap, which can then be stitched together into a vertical orthomosaic or even a 3D model. This information can then be used to detect defects such as cracks or other damage. For example, in case of building inspection, this can allow to more accurately estimate facade renovation costs and, after the repairs are finished - to check the quality of work of contractors.
Performing these types of inspection flights manually would be a difficult task for even the most experienced UAV pilots. This is the reason why most professional surveyors are moving towards automating it using popular flight planning software such as UgCS by SPH Engineering.
Fully automated drone vertical inspections are not only safer, they also allow for more precise data collection, which is very important for post-processing. Since drone surveys are repeatable with a high degree of accuracy, it allows the creation of a digital model of the structure after each survey flight, giving the ability to compare multiple models over time to see how the structure is changing, for example, monitor if any cracks are developing over time.
Workflow of planning vertical inspections using drones
Performing vertical inspections with drones can be divided into three phases - flight planning, execution, and post-processing.
Flight planning is started by drawing polylines on the map around the object. Next, the distance to the object is measured in the software and entered in the parameters. Similarly, the type of camera used and overlap parameters are entered by the operator along with minimum and maximum altitude values. Two inspection directions can be selected - horizontal or vertical. Vertical is more efficient for taller objects while horizontal is better for longer buildings.
The main parameter used when calculating the flight lines is the distance to the facade. The more accurately the flight is planned using polylines and maintaining a constant distance to the facade, the more consistent the ground sampling distance (GSD) of the end result will be.
Next camera actions are added. This allows to set the camera to automatically trigger either by time (every X seconds) or by distance (every X meters). Camera attitude action is added as well, setting a desired angle.
In cases when the structure is located on uneven terrain, it is necessary for the flight planning software to be able to plan the mission according to the terrain elevation model. By default in UgCS SRTM4 elevation data is used and it is possible to plan flights at a constant AGL (above ground level) altitude. Moreover, when doing centimeter-level precision flights very near to the side of a building, custom terrain elevation models imported from LiDAR scans can be used.
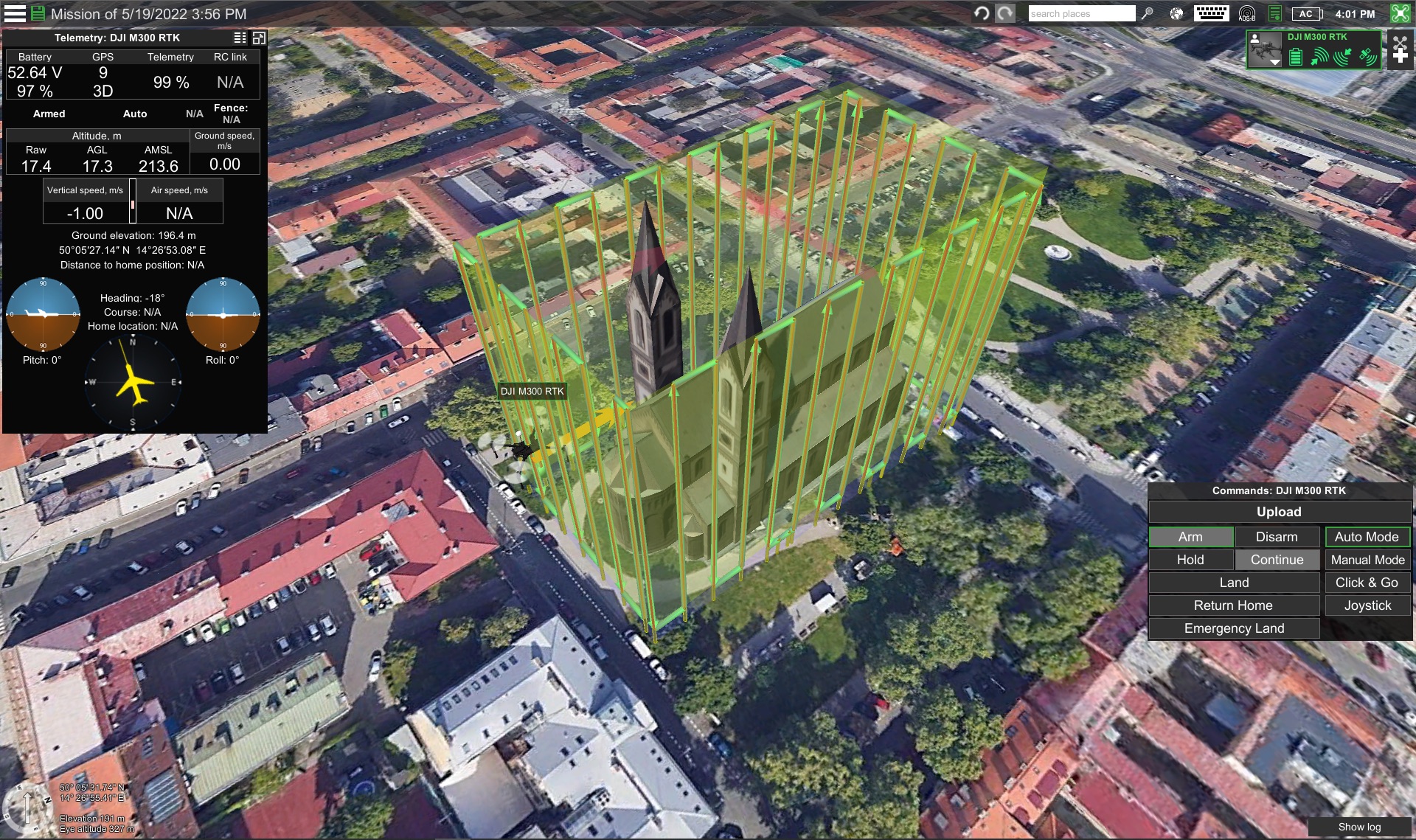
For flight execution, the planned route can be either executed from the desktop PC or downloaded offline on a mobile device or the drone’s smart controller so that the laptop does not need to be used in the field.
Useful tips/notes when performing vertical scans with drones
Firstly, it is important to remember than GPS signal quality may decrease when flying very close to a tall vertical building. Pilots should therefore always keep the drone RC in the hands and monitor the signal quality.
Secondly, in relation to the point above, it’s important to keep the drone in visual line of sight (VLOS). Since flight planning software such as UgCS allows to plan vertical scans where the drone goes around the corner of a building, the pilot should always follow the drone in these cases and not fly BVLOS. Alternatively, a visual observer, who is in direct communication with the pilot, may be used.
Why using drones on automated flights for vertical inspections is better
To summarize the points above, performing vertical drone surveys over manual surveys is better due to:
- Higher accuracy
- Repeatability of flights
- Increased crew safety
- Lower cost
Additional advantages of performing automated vertical inspections compared to manual drone inspection flights:
- Ability to maintain a constant ground sampling distance (GSD)
- Ability to maintain desired vertical and horizontal image overlaps
- Terrain following according to a digital elevation model (DEM)
Useful Links
- Discover the Vertical scan tool of UgCS »»»
- Detailed how-to instruction for a UAV vertical scan mission with UgCS »»»
- An application use case from Canada presented during the webinar UgCS for High-Resolution vertical inspections of the concrete arch dam with Niricson »»»