The main tasks covered by each type of inspection
In power line maintenance and safety, there are two main inspection approaches: Aerial Inspection, which monitors power line corridors and vegetation with advanced LiDAR equipment for quick data collection, and Fine Inspections, which carefully examines critical equipment and conductors with detailed route planning.
Aerial Inspections
Monitoring a long corridor of power lines and vegetation around them. Due to power outages being frequently caused by fallen trees or contact between trees and power lines, using LiDAR equipment for inspections becomes essential as it allows coverage of over 28 towers in just one day. Also, all necessary data is compilated within a few hours in the data processing software. Much faster and cheaper than usual visual or photogrammetry inspection.
Fine Inspections
This approach demands precise examinations of power line conductors and equipment. Accurate route planning is crucial to ensure that all critical points, such as conductors and insulators, receive a thorough inspection. This thorough approach helps identify and address potential issues and vulnerabilities in the power line system effectively.
UgCS, Professional drone mission planning software, simplifies data gathering on powerlines
3D Map, Diverse Elevations
UgCS provides a 3D map for planning missions with diverse elevations, allowing flight plans for large-scale missions and emphasizing sensor calibration.
LiDAR Corridor, Map Interaction
Users can create a LiDAR corridor flight plan by interacting with the map or configuring key parameters like corridor width, altitude mode, flight height, and sensor field of view. Adjusting the corridor width will determine the number of passes.
Calibration, High-Quality LiDAR
LiDAR IMU Calibration is vital for high-quality data collection. UgCS comes with in-built LiDAR IMU calibration tools such as figure-eight and U-shape, allowing one to automate this process during the flight preparation stage instead of having to do calibrations manually.
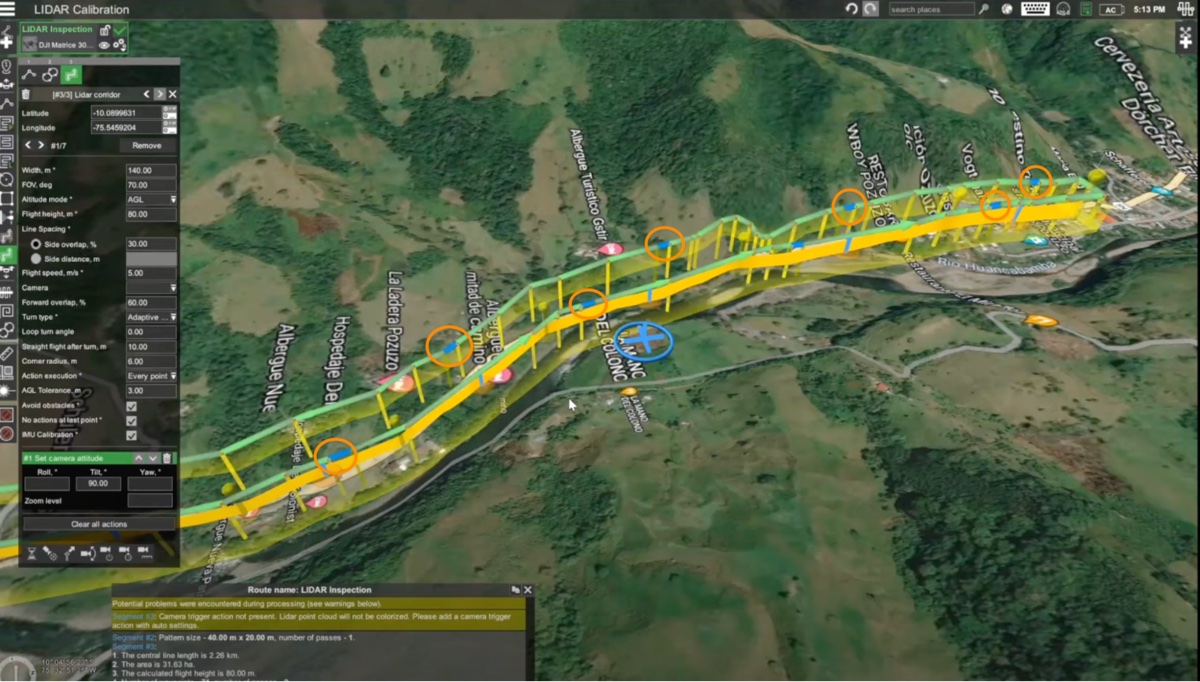
Data-processing
When the data is collected, it goes through post-processing using software such as LiPowerline, which provides real-time working condition analysis, simulations, and predictions.The post-processing software classifies the LiDAR data and identifies power lines, transmission towers, vegetation, and other features. It generates reports and analyzes conditions such as vegetation encroachment, wind effects, wire sag, and more.
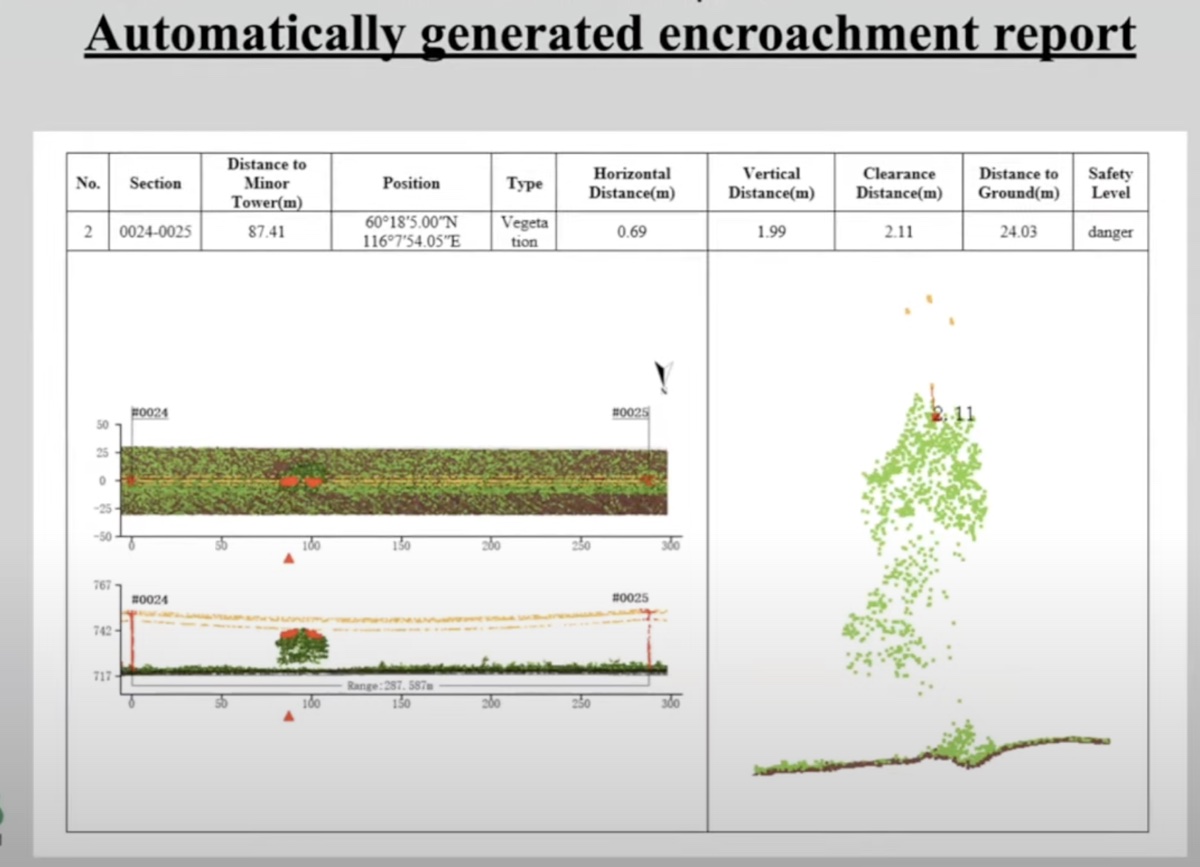
Vegetation encroachment and scissor crossings are done by predictive modeling, so it can predict future events from occurring future growths.Tree growth and tree fall prediction enable proactive and efficient risk management without the need for frequent revisits.
For Fine powerline inspections, point cloud data collected with UgCS is fed into LiPowerline. LiPowerline helps to generate camera positions and capture important tower components in high resolution for further visual inspection.
A short video with a brief demo of building the route for the Fine Inspection. Starts from 30:24
Image Inspector
When images of tower components are captured, they have to be converted into an actionable inspection report. Typically photos are placed in Word or PDF with little explanation.
To simplify this process, SPH Engineering has developed a simple tool for creating annotations to images - Image Inspector.
Benefits of Using ImageInspector Software
- Saves pilots a significant amount of time when creating reports
- Allows the pilot to annotate specific areas of an image, improving the final report's accuracy
- Allows pilots to tailor the report to their specific needs
- Helps pilots optimize future flights and reduce the number of shots required
How it works
The pilot
- takes high-resolution RGB or thermal images of the inspected asset, such as a power pole,
- uploads them to the ImageInspector software
- uses ImageInspector to annotate the images, marking specific areas of interest with severity levels and text comments
ImageInspector
- generates a customizable PDF report with annotations, severity levels, text comments, and image fragments
- exports camera positions and orientation to KML or DJI WPML for flight optimization.
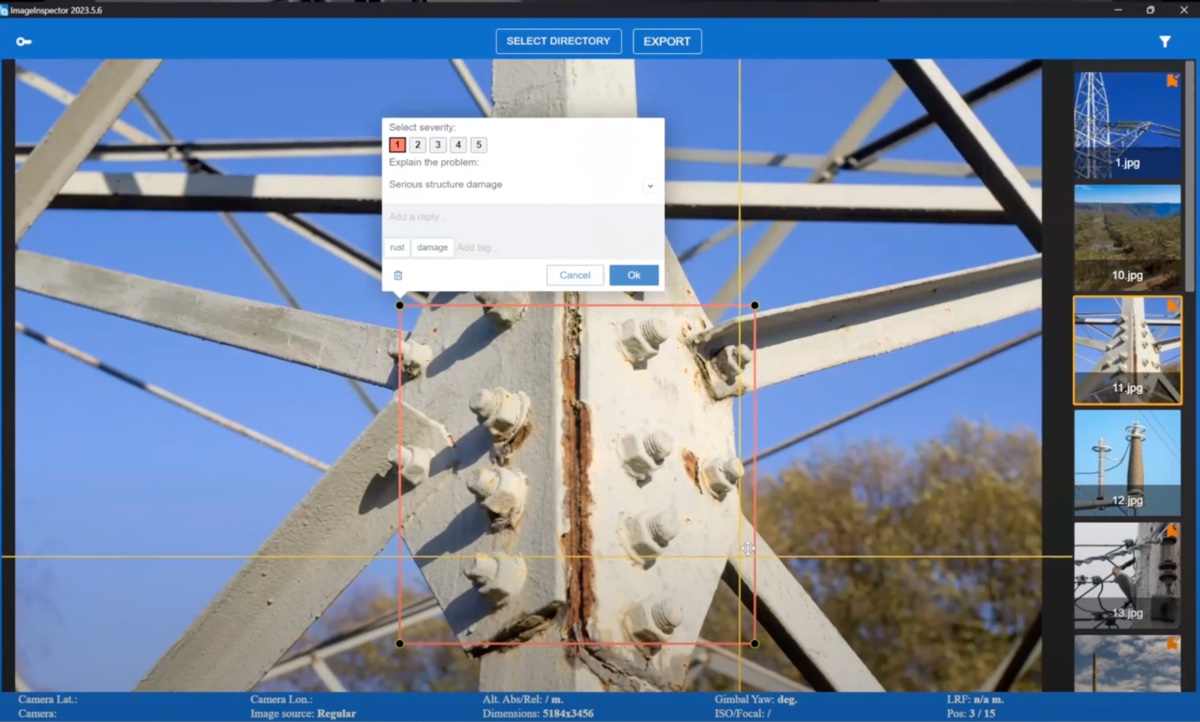
Conclusions
When analyzing drone inspections of power lines, careful attention should be given to data collection and processing methods. For those who have already integrated power transmission line inspections within their company, exploring ways to streamline or minimize the associated costs may be of great interest.
For a more detailed description of the tools recommended for powerline inspections in UgCS, please refer to this article and manuals.
Approach us at ugcs@ugcs.com to set up a drone inspection workflow in your company.
We will help with:
- proper software and hardware for your task
- building optimal data acquisition and data processing workflow
- organizing your data storage and sharing
Get your UgCS Trial and test unique features!
|| Article is written in collaboration with Green Valley International
|| Photo credits: Green Valley International
|| Watch the webinar “End-to-end Powerline inspections workflow explained” here: